
Do you know the three major requirements for sealing testing of automotive connectors?
Release time:
2022-10-11
1. Sealing test: It is required to test the sealing of the connector in a vacuum or positive pressure state. Generally, it is required to use a fixture to seal the product under a positive or negative pressure of 10kpa to 50kpa and conduct a gas tightness test. The leakage rate of the tested product shall not exceed 1cc/min or the higher requirement shall not exceed 0.5cc/min. Qualified products
1. Sealing test: It is required to test the sealing of the connector in a vacuum or positive pressure state. Generally, it is required to use a fixture to seal the product under a positive or negative pressure of 10kpa to 50kpa and conduct a gas tightness test. The leakage rate of the tested product shall not exceed 1cc/min or the higher requirement shall not exceed 0.5cc/min. Qualified products
2. Voltage withstand test: Voltage withstand test is divided into negative pressure resistance test and positive pressure resistance test. The test requires selecting an accurate proportional control valve group, and starting from the initial pressure value of 0, vacuum the product at a certain rate. The vacuum pumping time and the proportion of vacuum obtained can be adjusted. For example, set the vacuum extraction to -50kpa, and the extraction rate is 10kpa/min. The difficulty of this test is that the airtightness tester or leak detection instrument is required to be able to set the starting pressure for extracting negative pressure values, such as starting from 0, and of course, it can also be required to start from -10kpa, and the extraction rate can also be set and can be changed. Everyone knows that sealing testers or airtightness testers are equipped with manual or electronic pressure regulating valves, which can only be adjusted according to the set pressure. The starting pressure is from 0, and the ability to vacuum is generated by a vacuum source (vacuum generator or vacuum pump). The speed of vacuum pumping after the vacuum source passes through the pressure regulating valve is fixed, which means that it can only be extracted from 0 pressure instantly to the fixed pressure set by the pressure regulating valve, Does not have the ability to control the ratio of extraction pressure to time. The principle of positive pressure withstand test is similar to that of negative pressure withstand test, which is to set the starting pressure of positive pressure at any pressure, such as 0 pressure or 10kpa. The slope of pressure rise, also known as the slope, can be set, such as 10kpa/min: the test requires that the pressure rise be proportional to time and can be adjusted.
3. Rupture test (burst test): divided into negative pressure rupture test or positive pressure rupture test. The product is required to rupture instantly when vacuum is extracted or pressurized to a certain pressure range, and the pressure of rupture needs to be recorded. The difficulty of the test is that the negative pressure extracted by the airtightness tester meets the second test requirement, the pressure rate can be adjusted, and the pressure burst must be completed within the set range and cannot exceed this range. That is to say, blasting below or above this range does not meet the product testing requirements, and the testing pressure at this blasting point needs to be recorded. In actual testing, an anti riot device is required for this measurement. The usual anti riot device is to place the test workpiece in a pressure resistant stainless steel cylinder, which needs to be sealed. The stainless steel cylinder on the outer cover needs to be equipped with a high-pressure relief valve to ensure safety. When the explosion occurs, the fragments of the connector are scattered inside the pressure resistant stainless steel cylinder, which will not cause harm to personnel. From the above analysis, it can be seen that gas tightness testers generally require the design of three different devices to complete, and sealing leakage testing needs to be completed using a formed leak detector combined with a fixture system. Pressure test requires adding a proportional control valve group to accurately set the ratio of pressure value to time
Related News
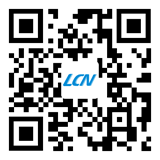
Mobile website
Shenzhen Linkconn Electronics Co., Ltd.
Tel:86-755-82943323
Fax:86-755-82966567
E-Mail:szlcn@linkconn.com
Add:15/F, Block E, China Resources Land Building, Hi-Tech Park, Nanshan District, Shenzhen, China
Copyright © 2023 Shenzhen Linkconn Electronics Co., Ltd.